-
Search
-
18046987606
Fiona@Robobeen.com
Manual vs Robotic Palletizer: What is the Future of Palletizing?
Every industry produces products in bulk. Stacking is essential to systematize and organize products for efficient storage and usage. This stacking is palletizing i.e. arranging products on shelves according to specific sequences or instructions. Conventionally, companies used to hire plenty of labor to perform palletizing manually. However, the emergence of robotic technology, primarily cobot (collaborative palletizing robot) technology, has had a revolutionary impact on this process. This blog post provides a comprehensive insight into the significant differences between manual and robotic palletizing, signifying the benefits of each category. Additionally, this post will highlight why businesses are switching to this approach.
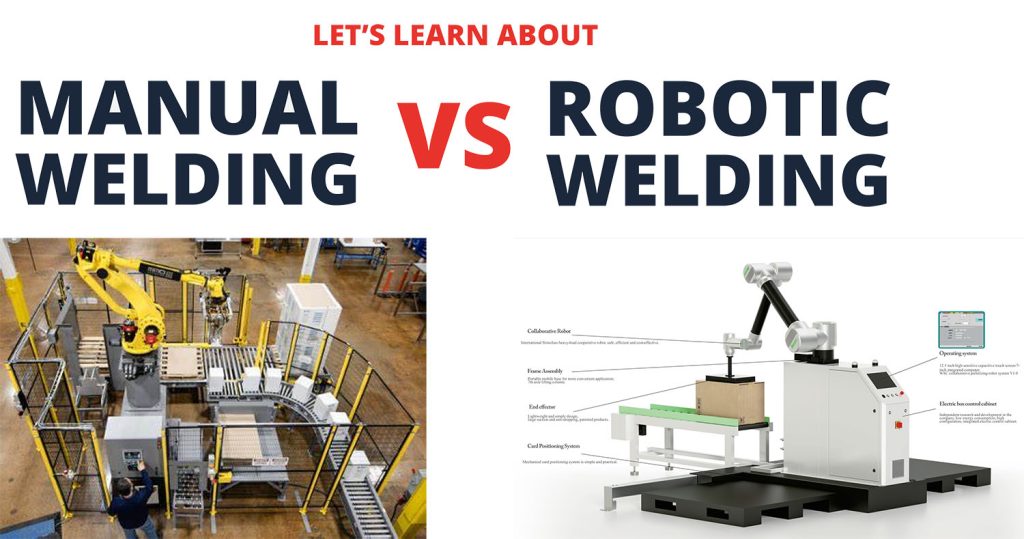
The Conventional Way: Manual Palletizing
Conventional palletizing used to rely on a physical workforce. Human labor was used to stack the products accordingly. Manual palletizing worked for decades, primarily in industrial sectors lacking automation, where labor was cheap and quickly available.
Exploring the Benefits of Manual Palletizing
Adaptability: Human laborers exhibit better adaptability as they can decide then and there without reprogramming. Humans can easily mold palletizing ways according to varying dimensions and weight of the product.
Cost Advantage for low-scale businesses: Manual palletizing offers a cost advantage to small-scale firms as there is no initial investment required. Small businesses enjoy this cost saving since you don't need to pay a hefty amount to set up entire robotic palletizing.
An easy money-paying skill: Manual palletizing is no rocket science. Labor can achieve it quickly through a few training sessions. So, if any individual has no formal education or needs a technical hand, manual palletizing can still be an option to earn some money.
The downside of Manual Palletizing
Potential health risk: For manual palletizing, each worker undergoes repetitive body moves such as bending, lifting, placing, and twisting. Such repetitive movements strain muscles, and a slight posture misalignment can result in chronic injuries. Thus, small companies may experience additional healthcare costs or an increased workforce absence.
To err is human: Manual palletizing is not error-free. Humans love chatting, and often, lack of attention due to any reason may result in inconsistent manual palletization. Such malpractices may damage products either during storage or transportation.
Inflation impacts labor cost: Labor cost is directly proportional to rising inflation. Manual palletizing may become a financial burden if the company has large-scale operations. Additional healthcare costs become inevitable.
Physical burnout: Manual palletizing eventually leads to physical weariness. The productivity of a labor palletizing manually naturally deteriorates over the years, leading to frequent errors and deteriorating productivity.
The New Era Approach: Robotic Palletizing
Robotic palletizing is the contemporary approach, where robots are replacing the physical workforce to stack up products. Using Cobots or collaborative robots is a win-win approach in the new era. In this palletizing strategy, robots co-work with humans, thus reaping the goodness of both methods, i.e., manual and robotic palletizing. Companies can now enjoy better productivity along with improved safety levels.
Exploring the Benefits of Robotic Palletizing
Better Productivity: Robots stay energized so they can work long hours without interrupting bathroom breaks or lunch breaks. Working at a uniform speed, they can finish more palletizing tasks faster than manual labor.
High accuracy: Robots are programmed by computers, so precision and accuracy are innate to their operations. The chances of errors are much less in robotic palletizing as they stay consistent with instructions.
Safety features: Cobots feature state-of-the-art technology and are well-suited to the safety of humans around them. They are hassle-free and can safely work with humans. Employing cobots can save companies from the burden of healthcare costs as it significantly mitigates the potential risks of injuries resulting from manual palletizing.
Cost-saving in the longer term: Normally, businesses operate on a going-concern basis. The decision of financial investment should be seen in a broader aspect. 6 months is the minimum time to witness the outcome of your investment, although some projects even take longer. The same goes for cobot technology. The initial investment may seem pricy, but in the long run, it may outweigh the cumulative effect of labor costs, associated healthcare costs, and damages incurred during transportation or human error. Companies can attain ROI in 6-12 months.
User-friendly: Palletizing cobots are super easy to use. Installation will take less than 5-10 minutes. Cobots' data storage and processing speed are way ahead of that of humans. They can easily store and retrieve 800+ receipts. It is just a matter of a single click.
Growth Potential: Cobots or robotic systems provide a convenient way of scalability. As soon as the company oversees rising operational needs, it can integrate more robotic units into the workforce. Unlike human labor, there is no need to provide training. Setting instructions is just a simple matter, and companies can enjoy sustainable results.
The downside of Robotic Palletizing
High Capex: Procuring and installing a cobot palletizing system is not a cup of tea. Instead, it requires high capex. Small businesses may need help managing it all financially.
Configuration requires expertise: Manual palletizing is not technical. However, robotic systems need an expert hand, which can be challenging. Kudos to intuitive interfaces and easy-to-use technology that simplifies the configuration issues. Today absolute touchscreen controls that can function in native languages have made lives more accessible than ever.
Lack of adaptability: Robots master repetition, yet lack adaptability like the human brain. As soon as a different handling situation arises, robots must be reprogrammed to act accordingly. However, new robots are integrated with AI and machine learning, thus adding as much flexibility as possible to these modern robotic systems.
Reasons to Consider Collaborative Palletizing
Cobots or collaborative palletizing robots provide the best workable solution. It combines the best aspects of both manual and robotic palletizing. Let's see what we can achieve from cobots.
Seamless integration: Cobots can seamlessly integrate into existing workflows. Since they do not require such safety measures, they can quickly work around humans, making them best suited for small—to medium-scale enterprises.
Early ROI: unlike conventional robots, companies get early returns from cobots. ROI will be in the form of more productivity and cost savings on labor and related healthcare.
State-of-the-art technology: Modern cobots have AI and machine learning capacity thus, they tend to adapt to any given circumstances accordingly
Diverting human capacities: If companies delegate programmable tasks to cobots, human resources can be diverted to more meaningful and complex tasks.
Conclusion
Both manual and robotic palletizing have their relevant pros and cons. There is no rule of thumb to declare the verdict. The decision to choose either of them will solely rely on specific business needs, scalability, and resources. While manual palletizing is light on the pocket for small-scale operations, it offers excellent flexibility. Robot palletizing, particularly cobot palletizing, is making groundbreaking achievements, yet we can expect this technology to be included at every scale of business. People might get even more budget-friendly cobots since collaborative palletizing provides an ultimate combo of both worlds