-
Search
-
18046987606
Fiona@Robobeen.com
Overview
The Delta Robot Pick and Place is an automation technology that is designed to address high speed precision in product placement. It can work at frequency of 60~120 times per minute, and the stroke can reach 1200mm, which can fully adapt to the present industrial requirement. Particularly well-suited for high-speed sorting, packing or placement applications, the Delta Robot is designed to boost performance in a range of industries.
With the future of smart manufacturing already in progress, ROBOBEEN can pride itself in being cutting – edge. The design of the Delta Robot Pick and Place is elite in combination with the high applicability and cost optimization, accuracy and looks which made it become indispensable in any production line.
The ZHIHUA series parallel robot that serves as the basis of this product has a unique configuration designed for XYZ translational motion and rotational motion about the Z-axis. This design provides high speed, compatibility, and simplicity of operation and maintenance that renders the design capable of application in almost any industrial processes.
Working Range(mm)
Configuration | |
Settings | Brand |
Servo Motor | Warsonco/Panasonic |
Machine Reducer | Nidec corporation/green |
Controller | Austria KEBA |
Applications:
✔ Pharmaceutical Industry: Ideal for at – high-speed sorting, and packing of pharmaceutical products conforming to the regulatory requirements and does not adversely affect the product characteristics.
✔ Food Industry: Effectively manages segregation and packaging of the food products to avoid contamination while at the same time enhancing the flow of production.
✔ 3C (Computers, Communications, and Consumer Electronics): Designed for putting together and packing electronics parts so as to minimize handling periods in high technology situations.
✔ Daily Chemicals: Responsible for arranging and packing daily chemical products so as to ensure that the packaging is well done and that this is done in harmony with the high rates of production.
✔ Hardware Sorting: Designed for sorting and packing of different hardware components and exhibiting good results with any type of product.
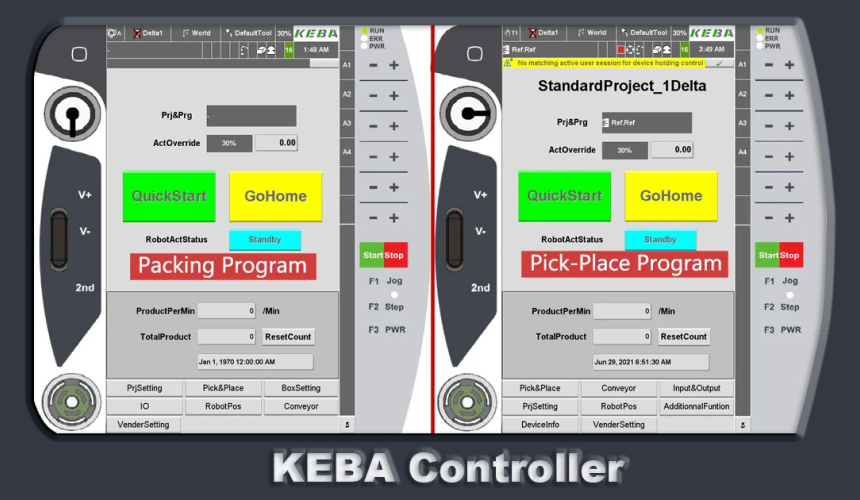
Features
✔ Unique Spring Design: Includes a small spring device that serves not only as an additional mechanism to increase the robot’s service life but also increases operational safety.
✔ High Rotation Accuracy: The fourth axis of the robot secures remarkable rotational stability with the accuracy of 0. 05 degrees of freedom which in turn makes it possible to achieve very delicate and fine motion as it is required in ✔ various high accuracy operations.
✔ Inverted Installation Capability: However, the robot can also be mounted in an inverted fashion, with excellent tracking characteristics offered and the system is fully adaptable for different production arrangements.
✔ Cost-Effective Solution: Able to deliver a high performance at the relatively low price point with a visual dynamic tracking, to improve the business processes and minimize the overall time loss.
✔ Strong Performance: The robot has great bearing capacity; it is very rigid with better dynamic characteristics. This makes it capable of carrying heavy loads while perform at optimum level or at the highest level possible.
✔ Lightweight Design: Reduced self-weight load ratios make it easier for the robot to handle the products without putting excessive stress on them thus enhancing the robot’s durability.
Specifications
Parameters | |||
Model | WSC-1200D-L3 | WSC-1200D-L8 | WSC-1200D-L12 |
Power Rating | four-axis | four-axis | four-axis |
Max Load(kg) | 3kg | 8kg | 12kg |
Standard Cycle Time(s) | 0.4 seconds/cycle (25/305/25 mm) | 0.4 seconds/cycle (25/305/25 mm) | 0.4 seconds/cycle (25/305/25 mm) |
Repeat Positioning Accuracy(mm) | ±0.05mm | ±0.05mm | ±0.05mm |
Angular Positioning Accuracy | 0.05° | 0.05° | 0.05° |
Power | 220V-240v 50/60Hz | 220V-240v 50/60Hz | 220V-240v 50/60Hz |
Power Rating | 2.5kw | 3.5kw | 5kw |
Noise Level | <75db | <75db | <75db |
Protection Level | IP54 | IP54 | IP54 |
Motor Method | AC servo drives | AC servo drives | AC servo drives |
Demonstrator | 7-inch demonstrator | 7-inch demonstrator | 7-inch demonstrator |
Vision Positioning Module | Optional configuration (130W camera, lens, light Source) | Optional configuration (130W camera, lens, light Source) | Optional configuration (130W camera, lens, light Source) |
Operating Instructions | PTP, LINE, PICK, PLACE | PTP, LINE, PICK, PLACE | PTP, LINE, PICK, PLACE |
Installation Method | Inverted | Inverted | Inverted |
Robot Weight | 72kg | 72kg | 72kg |
Playlay load 0.1kg | 0.42s | ||
Playlay load 1kg | 0.49s | ||
Working Temperature | 1-40°C | ||
Humidity Range | 5%~90%(No condensation) | ||
Life Span | 20000 hours+ | ||
GW | 74kg | ||
1-3rd Axis Motor (if) | Panasonic | ||
The Fourth Axis motor (then) | Panasonic | ||
1-3rd Axis Reducer/Gearbox(if) | Harmonic/Nidec | ||
The Fourth Reducer/Gearbox(then) | Leader drive | ||
Controller/PLC | Keba | ||
HMI | Keba |