-
Search
-
18046987606
Fiona@Robobeen.com
Conventional Vs Robotic Palletizing: Which is Right for Your Business?
Conventional vs. Robotic Palletizing comparison, Palletizing is a critical process in the logistics and manufacturing sectors. It involves stacking products onto pallets for storage, shipping, or distribution. Traditionally, this task has been accomplished manually or with conventional palletizing systems. However, advances in automation technology have seen the emergence of robotic palletizing as a viable and increasingly popular alternative. This article will compare traditional and robotic palletizing, exploring their pros and cons, and how to choose the right system for your business.
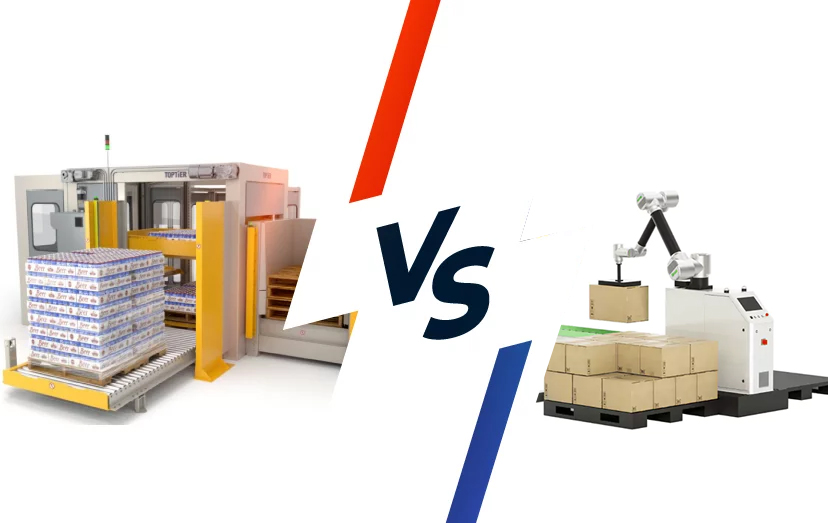
1.0.Understanding Conventional Palletizing
Conventional palletizing systems typically use mechanical systems such as conveyors, sensors and gantries to stack products onto pallets. These systems have been used for decades and are known for their reliability and consistency in handling large quantities of uniform products.
Advantages of Conventional Palletizing:
Proven technology: Traditional systems have been proven for decades, with stable performance and outstanding performance in various industries
High-Speed Operation: Capable of handling high-speed operations, these systems are ideal for environments that require rapid stacking of large quantities of identical products
Lower initial cost: Traditional systems typically have lower upfront costs than robotic palletizing, making them more affordable for smaller businesses.
Simplicity: Traditional systems are relatively simple in design and operation, easier to maintain, and have fewer operational challenges.
Drawbacks of Conventional Palletizing:
Limited flexibility: Traditional systems are designed for specific tasks and may have difficulty handling products of different sizes, shapes or weights
Limited flexibility: Traditional systems are designed for specific tasks and may have difficulty handling products of different sizes, shapes or weights
High maintenance requirements: Due to the mechanical nature of traditional systems, they require regular maintenance to prevent breakdowns, which can increase costs in the long run.
2. Understanding Robotic Palletizing
Robotic palletizing uses a robotic arm to pick up and place products onto pallets. These systems are highly programmable, providing great flexibility and precision. Robotic palletizing systems can be equipped with advanced sensors, cameras, and software according to scenario requirements, and can handle products of various shapes, sizes, and weights.
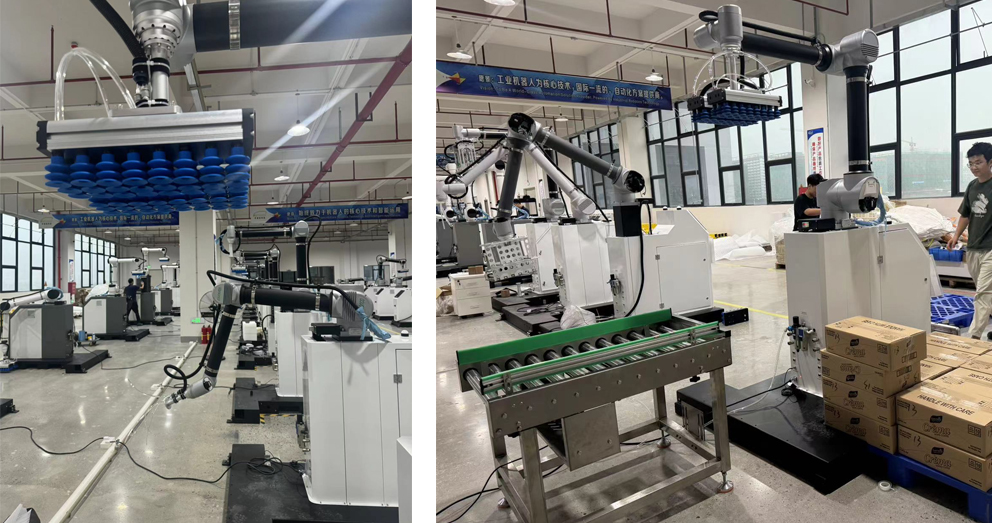
Advantages of Robotic Palletizing:
Flexibility: Our palletizing robots are suitable for different types of production products according to the needs of production scenarios. They can be connected to different production lines, and can realize single-grip, double-grip, triple-grip or quad-grip at a time. They can also connect to two production lines at a time. The highest palletizing can reach 2.4 meters. The small size can be flexibly moved.
Simple operation: Our robots do not need to be programmed or installed. The path can be set in 5 minutes. The full touch screen makes the vision more intuitive and supports small language systems. More than 800 paths can be stored and directly called out for use without repeated editing.
High flexibility: Our palletizing robots are space-efficient: Compared with traditional systems, robotic palletizing usually takes up less space, which is very suitable for factories with tight space.
Improved safety: By automating the palletizing process, the robotic system reduces the need for manual operations in potentially dangerous environments, thereby improving workplace safety.
Scalability: The robotic system can be easily expanded or reduced according to production needs, providing a sustainable solution for the future growth of the enterprise.
Lower long-term costs: Although the initial investment of robotic palletizing is higher, the long-term operating costs are lower due to reduced maintenance requirements, improved energy efficiency and reduced downtime. The investment can be recovered within half a year to one year
Drawbacks of Robotic Palletizing:
High initial cost: The initial cost of a robot system can be significantly higher than a traditional system, which can be a barrier for small businesses. However, our robots have also been structurally optimized to reduce development costs. Compared with industrial robots, our collaborative palletizing robots are more priced to meet the needs and development of small and medium-sized enterprises.
Complexity: Industrial robot systems are more complex and may require expertise for programming, maintenance, and troubleshooting. However, our collaborative palletizing robots perfectly avoid this shortcoming and are easy to operate, and do not require programming.
3. Key Considerations When Choosing Between Conventional and Robotic Palletizing
When deciding between Conventional robotic palletizing, there are several factors to consider to ensure you choose the system that best meets your needs.
1. Product Variety and Volume:
If your business handles large volumes of uniform products, a traditional system may be more cost-effective and efficient.
For operations involving diverse product types, sizes, or frequent packaging changes, robotic systems provide the flexibility needed to handle these changes.
2. Budget:
Traditional systems typically have a lower initial cost, making them a viable option for businesses with limited budgets.
While robotic systems require a higher upfront investment, the long-term savings in maintenance, energy, and labor costs can prove their worth.
3. Space Availability:
Conventional palletizers usually require more space due to mechanical components and layout.
Robotic palletizers are compact in design and suitable for factories with limited space.
4. Workforce and safety
If labor costs are an issue, or workplace safety is a priority, robotic systems can significantly reduce the need for manual handling, thereby reducing the risk of injury.
Conventional systems may require more human intervention, especially in high-speed operations, increasing the potential risk of workplace accidents.
5. Maintenance and downtime:
Due to their mechanical nature, traditional systems typically require more frequent maintenance, which can result in higher long-term operating costs.
While robotic systems require professional maintenance, they typically have fewer parts, less wear and tear, and less downtime.
Case Study: Conventional and Robotic Palletizing in Action
To better illustrate the difference between traditional palletizing and robotic palletizing, here are two real-life examples:
Case 1: Beverage Industry
A beverage company had a high-volume production line and needed a palletizing solution for uniform bottles. The company chose a conventional palletizing system due to its high speed and reliability. The system handles thousands of bottles per hour, palletizing quickly and efficiently with little to no customization required.
Case 2: E-commerce distribution center
An e-commerce distribution center that handles a wide range of products, from small electronics to large household items, chose a robotic palletizing system. The flexibility of the robotic arms enables the center to palletize products of various shapes and sizes, accommodating different packaging needs without frequent reprogramming.
5. The future of palletizing: hybrid systems
As technology advances, hybrid palletizing systems that combine the advantages of traditional and robotic systems are emerging. These systems offer the high speed of traditional systems and the flexibility of robotic palletizers, providing a balanced solution for companies with diverse needs.
Conclusion
Choosing between conventional or robotic palletizing depends on several factors, including your product type, production volume, budget, and space constraints. Conventional systems offer reliability and speed for uniform products, while robotic systems offer speed for multiple