-
Search
-
18046987606
Fiona@Robobeen.com
Collaborative Palletizing vs Traditional Palletizing: Which One is Best?
Shaping the Future of Logistics and Manufacturing
As we can see from the dynamic changes in the structure and requirements of the industrial environment, the request for collaborative palletizing production efficiency, safety, and adaptability is more important now than it was ever before. It can make industries as diverse as the food and beverage service and e-commerce able to work more efficiently, effectively, and safely, while achieving the right cost.
How Collaborative Palletizing Works?
In collaborative palletizing, there are the cobots, which are information technology, sensors, software and robotics machinery. These cobots can be easily incorporated with other systems where they provide options for movement control and feedback mechanisms.
Vision Systems:
Uninterrupted interaction between humans and cobots can be facilitated by the use of vision systems whereby the cobot identifies and positions the product in the production line. This kind of visioning system allows for the issue of a better grip depending on the form, size, and position of the object to allow for efficiency in palletizing.
Force Sensors:
To keep safety and accuracy in mind, these robots are programmed with force sensors that will enable the robot to sense external force. This feature is mandatory where human-bound workers are involved as it eliminates the chances of a collision or an accident.
Software Integration:
Automotive collaborative palletizing systems come with superior software that enables easy programming of the systems. Most of these systems also have friendly graphical interfaces through which operators can schedule tasks without much training.
Features of Collaborative Palletizing Optimizing Workload Productivity and Versatility:
The efficient palletizing solutions not only stand for user-friendliness, but we also provide ways to adapt the palletizing systems to their particular industries’ practices. There is the factor of ease of installation and the ease of readjustment among some of the beneficial features of the system. These systems can further be fitted and reconfigured within just two hours, thus making it possible to have minimal interruption time during various conversions.
Beneficial Features:
- This quick adaptability also ensures that the production flows can easily adapt to contingencies as may be required by the market forces. In terms of efficiency, the collaborative palletizers provide a high stacking speed, 8-11 boxes per minute which is rather important for industries that work with high volumes of products.
- These systems also provide a long path capacity that may reach up to 800 stacking paths that are best suited for wide-stacked applications. Also, they support maximum tray dimensions of 1400mm x 1400mm so that businesses can manage different forms of products effectively.
- Another feature is dual working product positions in which two products can be stacked at the same time increasing output. Where orientation of products is desirable in industries, the label orientation function helps in proper positioning on pallets with minimal chance of error in positioning the pallets.
Through the use of these features, various sectors of the economy can improve efficiency and minimize on cost of hiring workers to conduct manual tasks. For further information on this kind of palletizing approach, visit the Robobee guide on automation.
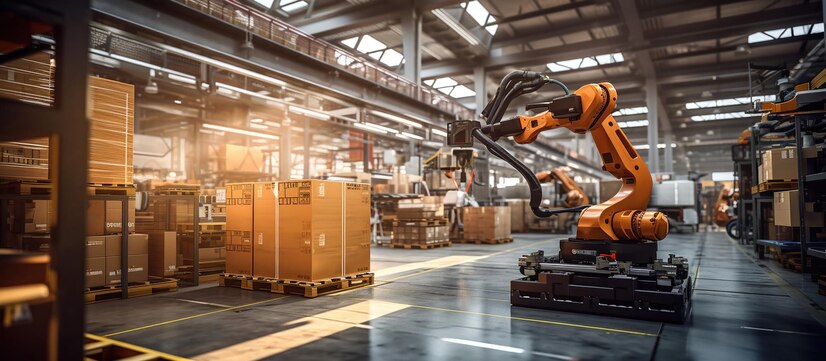
Collaborative Palletizing vs Traditional Palletizing:
Comparing the process of collaborative palletizing to conventional ways of achieving the same goal it becomes understandable why organizations are choosing collaborative palletizing means. Conventional palletizing methods that are currently in use are not effective but are characterized by high fixed costs for the structures and protective casings. It is, therefore, possible to conclude that RoboBee palletizers are more cost-effective and flexible compared to traditional palletizers.
Space Utilization: These palletizers do not require large safety barriers as collaborative robots do; therefore, they occupy considerably less space, which could be a great advantage if the facility has limited floor space to work with or if the business is small.
Cost Savings: The cobots are relatively cheaper in installation and cost of maintenance compared to the other industrial robots. This also makes them reusable and hence easily reallocated to other functions to save on long-term running expenses.
Ease of Integration: Most cobots are basically so the setup duration is taken into account most of the time. Organizations can adopt collaborative palletizing solutions with disruption to the flow of operations.
Robotic Palletizing Solutions for Manufacturing by RoboBee
The company RoboBee is at the cutting edge of robotic palletizing offerings to the manufacturing industry. As companies continue to pressurize industries for faster, better, and more accurate processes, RoboBee systems provide unprecedented solutions for pallet operations. Our advanced systems are developed for various products to be moved in varieties of small items to heavy items and thus be fitted to various manufacturing industries.
Key Features of RoboBee Robotic Palletizing
• High Efficiency: This can be done per minute and in a sequent manner to allow the stacking of several products at once thus increasing throughput.
• Customizable: Integration with different production lines is possible and easy as the device can fit into almost any existing lines.
• Improved Safety: Developed with adjacencies for coexistence between humans and robots on economic productivity and safety from mishaps.
• Flexible Handling: Flexible in size and form hence could be used in complicated production processes of products of different sizes and shapes.
Unlocking the Potential of Collaborative Palletizing
Our collaborative palletizing robots are designed to address emerging production needs and global supply chain requirements to increase operational effectiveness while improving accessibility. As such, they are ideal for automating palletizing processes, especially for organizations that require complex processes in the production line. Another interesting aspect of the cobots is the rate at which they can stack the products. This makes them more preferable for industries that have many products and need frequent turnover. Regardless of the type of application, be it in manufacturing, warehousing, and logistics the robot is a proven solution to tackle high-capacity requirements.
- It should be noted that these cobots are developed not only for performance but also for convenience. It is a highly effective device and has a low set-up time that makes its use easy. A unique advantage to industries is the short implementation period so that they begin seeing better performances in productivity.
- Palletizing cobots are very accurate and swift in handling the processes, thus we cut down on manual effort, and several mistakes and enhance the ROIs thereby getting a better bottom line. We are the best for any firm that intends to operate in the current environment that is deemed as being highly dynamic. To discover the latest palletizing solutions and the advantages that they can bring to your company, get in touch with Robobee automation solutions.
Conclusion:
Collaborative palletizing is transforming the way industries approach automation. With its combination of safety, efficiency, flexibility, and cost-effectiveness, it is rapidly becoming the preferred choice for businesses looking to enhance their palletizing processes. For more information on the latest in collaborative palletizing solutions, be sure to check out our detailed on RoboBee.